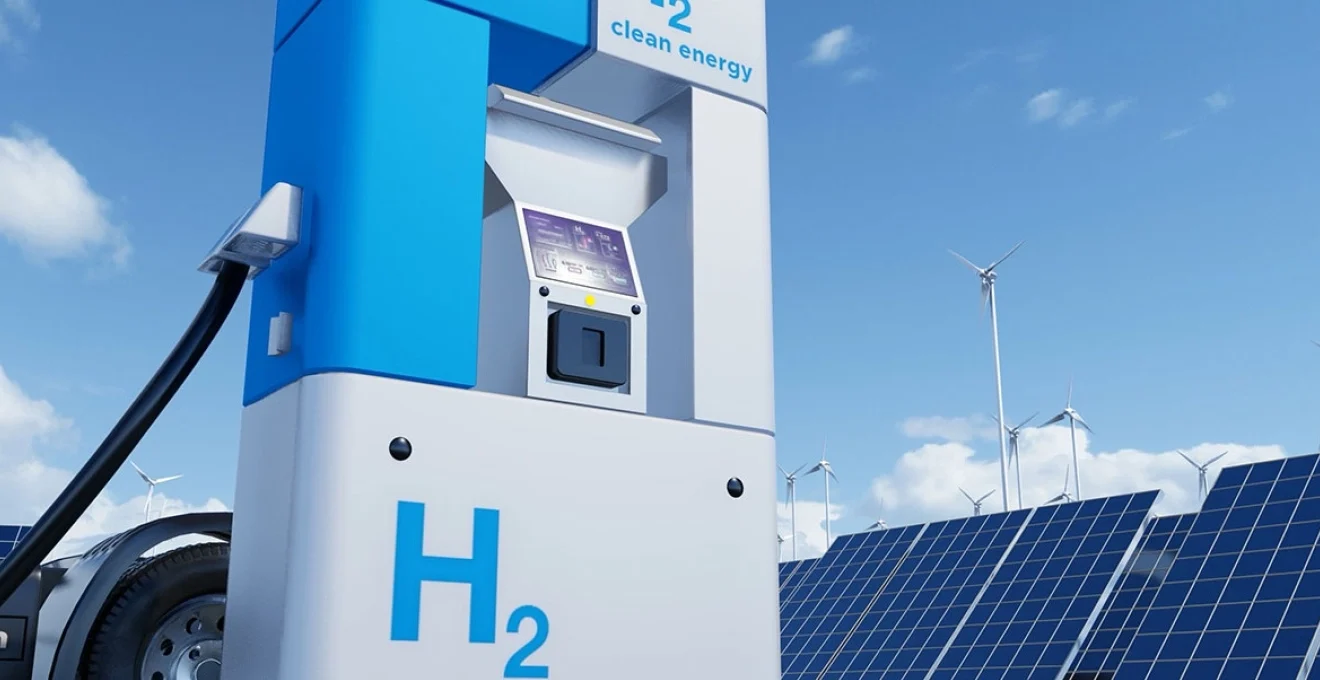
The global energy landscape is witnessing a remarkable transformation as hydrogen emerges as a versatile and promising energy carrier. With zero direct emissions at point of use and multiple production pathways, hydrogen represents a critical component in our transition toward a more sustainable energy future. Its unique properties allow it to serve as both a clean fuel and an energy storage medium, addressing intermittency issues inherent in renewable energy sources like wind and solar. The versatility of hydrogen enables applications across various sectors including transportation, industrial processes, power generation, and residential heating – areas where direct electrification faces significant challenges.
As climate change concerns intensify and nations worldwide commit to carbon neutrality targets, hydrogen's role has evolved from a niche solution to a centerpiece of energy strategies. This clean energy carrier offers a pathway to decarbonize hard-to-abate sectors while providing flexibility to our energy systems. The hydrogen color spectrum – from green (produced via renewable electricity) to blue (from natural gas with carbon capture) – presents different approaches to its production, each with distinct environmental footprints and technological readiness levels.
Hydrogen production technologies for green energy applications
The methods used to produce hydrogen significantly impact its environmental benefits and economic viability. Currently, most hydrogen is produced from fossil fuels, primarily through natural gas reforming, accounting for approximately 76% of global dedicated hydrogen production. However, low-carbon production methods are gaining momentum as technology advances and costs decline. The selection of appropriate production technology depends on factors including available resources, infrastructure, energy prices, and environmental considerations.
Renewable-powered electrolysis, or "green hydrogen," represents the most environmentally beneficial production method with near-zero emissions across the entire value chain. Biomass gasification offers another renewable pathway, particularly valuable when combined with carbon capture technologies. Meanwhile, fossil-based production with carbon capture and storage ("blue hydrogen") provides a transitional solution that leverages existing infrastructure while significantly reducing emissions compared to conventional methods.
Each hydrogen production pathway presents unique advantages and limitations that must be evaluated within specific contexts. For instance, electrolysis requires substantial renewable electricity, but yields extremely pure hydrogen suitable for sensitive applications like fuel cells. Steam methane reforming, while currently more economical, faces challenges in a carbon-constrained world unless paired with effective carbon capture solutions. These technological considerations shape investment decisions and policy frameworks aimed at developing hydrogen infrastructure, and you can find out more here.
Electrolysis systems: PEM vs. alkaline vs. solid oxide methodologies
Electrolysis, the process of splitting water molecules into hydrogen and oxygen using electricity, represents the cornerstone of green hydrogen production. Three main electrolysis technologies dominate the market, each with distinct operational characteristics and applications. Proton Exchange Membrane (PEM) electrolyzers operate at lower temperatures (50-80°C) and offer rapid response times, making them ideal for integration with variable renewable energy sources. Their compact design and high current density provide space efficiency, though they typically require precious metal catalysts like platinum and iridium.
Alkaline electrolyzers, the most mature and commercially available technology, operate at similar temperatures but use potassium hydroxide as an electrolyte. These systems offer lower capital costs and avoid precious metals, using nickel-based catalysts instead. However, they respond more slowly to power fluctuations and operate at lower current densities, resulting in larger physical footprints. Their technological maturity makes them a reliable choice for large-scale, steady-state operations.
Solid Oxide Electrolysis Cells (SOEC) represent the emerging frontier, operating at significantly higher temperatures (700-850°C). This elevated temperature reduces electricity requirements by harnessing thermal energy to drive reactions, potentially achieving electrical efficiencies exceeding 80%. While still in early commercialization, SOECs offer promising pathways for integration with industrial processes that generate waste heat, creating valuable synergies in energy systems.
Electrolysis technologies are advancing rapidly, with system efficiencies improving and capital costs declining. The growing scale of manufacturing and deployment is driving this progress, with PEM systems seeing particularly rapid advancement as renewable integration expands.
The selection between these technologies depends on specific application requirements, including response time needs, available energy sources, space constraints, and operational parameters. Many large-scale projects now implement hybrid systems that leverage the complementary strengths of different electrolyzer technologies to optimize overall system performance across varying operational conditions.
Solar-driven hydrogen production through photocatalytic water splitting
Photocatalytic water splitting represents an elegant approach to hydrogen production that directly harnesses solar energy without the intermediate electricity generation step required by conventional electrolysis. This process employs specialized semiconductor materials that absorb photons and generate electron-hole pairs, which then facilitate water-splitting reactions on the catalyst surface. The direct conversion offers theoretical efficiency advantages by eliminating conversion losses associated with separate photovoltaic and electrolysis systems.
Current research focuses on developing semiconductor materials with appropriate band gaps and stability in aqueous environments. Titanium dioxide remains the most studied photocatalyst due to its stability and low cost, though its wide band gap limits solar spectrum utilization. Recent advances have explored doped materials, heterostructures, and quantum dots to expand light absorption ranges and improve charge separation efficiency.
Despite promising laboratory results, photocatalytic systems face significant challenges in scaling to commercial applications. Low solar-to-hydrogen conversion efficiencies – typically below 5% in practical systems – necessitate large collection areas. Additionally, many high-performance catalysts contain rare or precious metals, introducing cost and sustainability concerns for widespread deployment.
Artificial leaf concepts represent an integrated approach to photocatalytic hydrogen production, mimicking natural photosynthesis in self-contained devices. These systems incorporate both light-harvesting and catalytic components in configurations designed for practical hydrogen collection, potentially offering simplified deployment compared to centralized production facilities.
Biological hydrogen generation with cyanobacteria and green algae
Biological hydrogen production harnesses natural metabolic processes in microorganisms to generate hydrogen from water and sunlight or organic substrates. Photobiological production employs photosynthetic microorganisms like cyanobacteria and green algae that can redirect electron flow from photosynthesis to hydrogen production under specific conditions. These living catalysts operate at ambient temperatures and pressures, utilizing abundant materials and self-replicating to reduce system complexity.
The two primary biological pathways include direct and indirect photolysis. Direct photolysis couples water splitting directly to photosynthetic electron transport, while indirect approaches involve intermediate carbon fixation followed by hydrogen production under dark, anaerobic conditions. Both pathways employ hydrogenase or nitrogenase enzymes that catalyze proton reduction to molecular hydrogen.
Current biological systems face efficiency limitations, with solar conversion efficiencies typically below 1%. Oxygen sensitivity of hydrogenase enzymes presents a fundamental challenge, as photosynthetic oxygen production inhibits hydrogen evolution. Research approaches include genetic engineering to develop oxygen-tolerant hydrogenases, temporal separation of oxygen and hydrogen production phases, and spatial separation using membranes or compartmentalized bioreactors.
Dark fermentation provides an alternative biological pathway that generates hydrogen from organic substrates without light input. This process can utilize waste biomass, creating valuable synergies with waste management systems while producing biohydrogen. Combined systems that integrate photobiological and fermentative processes show promise for maximizing hydrogen yields from available resources while addressing waste treatment needs.
Steam methane reforming with carbon capture for blue hydrogen
Steam Methane Reforming (SMR) currently dominates global hydrogen production, accounting for approximately 76% of dedicated production capacity. This well-established process reacts natural gas with high-temperature steam (700-1000°C) over a nickel-based catalyst to produce synthesis gas (hydrogen and carbon monoxide), followed by the water-gas shift reaction to increase hydrogen yield. While mature and economically competitive, conventional SMR releases significant CO₂ emissions – typically 9-12 kg CO₂ per kg hydrogen.
Blue hydrogen introduces carbon capture, utilization, and storage (CCUS) technologies to conventional SMR, capturing 50-95% of process emissions. Pre-combustion capture targets the concentrated CO₂ stream from the process gas, while post-combustion systems capture emissions from the SMR furnace. Advanced configurations like Auto-Thermal Reforming (ATR) or partial oxidation create more concentrated CO₂ streams that simplify capture processes.
The carbon intensity of blue hydrogen depends critically on capture rates and upstream methane emissions. High capture rates exceeding 90% require integration of multiple capture technologies addressing different emission sources within the production facility. Equally important is minimizing methane leakage throughout the natural gas supply chain, as methane's potent greenhouse effect can significantly undermine climate benefits if not properly managed.
Blue hydrogen represents a pragmatic near-term pathway leveraging existing natural gas infrastructure while significantly reducing carbon emissions. Its role in a clean energy transition depends on achieving very high capture rates, controlling fugitive methane emissions, and ensuring permanent CO₂ storage. As a transitional solution, it enables hydrogen market growth while green production technologies mature and scale to meet increasing demand.
Storage solutions and infrastructure development
Hydrogen's low volumetric energy density presents significant storage challenges that must be overcome for widespread adoption. At ambient conditions, hydrogen occupies substantially more volume than conventional fuels for equivalent energy content – approximately four times more space than natural gas. This fundamental property necessitates compression, liquefaction, or chemical bonding to achieve practical storage densities for transportation and stationary applications.
Infrastructure development represents a classic "chicken and egg" challenge: demand for hydrogen depends on available infrastructure, while infrastructure investment requires assured demand. Strategic approaches to resolve this include industrial clusters where production and high-volume industrial users share infrastructure, hydrogen valleys integrating multiple applications within defined geographic regions, and strategic corridor development along major transportation routes.
Storage requirements vary dramatically across applications and scales, from high-pressure tanks in vehicles to massive seasonal storage in geological formations. Each storage method presents distinct advantages and limitations regarding energy density, cost, discharge rates, and safety considerations. The optimal solution depends heavily on specific use cases, with many systems implementing complementary storage technologies to address different operational requirements.
Storage Method | Energy Density (MJ/kg) | Key Advantages | Major Limitations |
---|---|---|---|
Compressed Gas (700 bar) | 5-6 | Mature technology, fast refueling | Low volumetric density, high compression energy |
Liquid Hydrogen (-253°C) | 8-10 | Higher density, established in industry | High liquefaction energy, boil-off losses |
Metal Hydrides | 0.5-2 | Safe operation, moderate pressure | Heavy systems, thermal management needed |
Geological Storage | N/A (site-specific) | Massive capacity, seasonal storage | Limited geological suitability, high capital cost |
High-pressure composite tanks and type IV storage systems
High-pressure gas storage represents the most widely deployed hydrogen storage technology, particularly for mobility applications. Modern composite tanks operate at pressures of 350-700 bar (5,000-10,000 psi), balancing storage density with practical engineering constraints. Type IV tanks, featuring a polymer liner fully wrapped with carbon fiber composite, offer the highest performance for mobile applications by minimizing weight while maintaining structural integrity under extreme pressures.
The evolution of high-pressure storage has progressed through multiple design generations. Early metallic tanks (Type I) have given way to composite-wrapped designs that reduce weight while maintaining or improving safety margins. Type IV tanks eliminate all metal structural components, maximizing gravimetric energy density – a critical parameter for vehicle applications where every kilogram impacts range and efficiency.
Manufacturing advancements in carbon fiber winding technology, optimized resin systems, and non-destructive testing methods have dramatically improved tank performance while reducing costs. Current research focuses on novel fiber materials, automated production techniques, and conformable tank geometries that better utilize available vehicle space. These improvements are essential for achieving cost targets that enable mass-market adoption of hydrogen vehicles.
Safety features in modern storage systems include multiple redundant protections such as thermally-activated pressure relief devices, impact sensors, and sophisticated monitoring systems. These technologies have enabled exemplary safety records in real-world deployments, with hydrogen vehicles demonstrating safety performance comparable to or exceeding conventional vehicles in crash scenarios and fire events.
Metal hydride storage materials: LaNi5 and TiFe compounds
Metal hydride storage offers a unique approach to hydrogen containment, utilizing the ability of certain metals and alloys to absorb hydrogen atoms within their crystal lattice. This chemical bonding allows hydrogen storage at moderate pressures and near-ambient temperatures, significantly improving safety profiles compared to high-pressure or cryogenic systems. The hydrogen atoms occupy interstitial sites in the metal lattice, achieving volumetric densities that can exceed those of liquid hydrogen.
LaNi₅ compounds represent one of the most studied metal hydride families, offering reversible hydrogen storage at near-ambient conditions. These materials absorb hydrogen at modest pressures (2-10 bar) and release it when heated slightly above room temperature, creating a convenient operational window. Their excellent cycling stability and fast kinetics make them suitable for applications requiring frequent charge-discharge cycles, though their relatively high cost limits deployment to specialized applications.
TiFe-based alloys offer a more economical alternative using abundant elements. These materials operate at slightly higher pressures but substantially reduce material costs compared to rare-earth containing compounds. Modifications with manganese, nickel, or zirconium can tune operating parameters to match specific application requirements. Recent developments have addressed historical challenges with activation and impurity sensitivity, expanding their practical application potential.
Thermal management represents a critical aspect of metal hydride systems, as hydrogen absorption releases heat (exothermic) while desorption requires heat input (endothermic). Practical systems incorporate heat exchangers and thermal management strategies to maintain optimal operating temperatures. Advanced designs integrate this thermal requirement as an advantage, creating heat pump effects or thermal energy storage capabilities that complement the primary hydrogen storage function.
Liquid hydrogen cryogenic infrastructure by air liquide and linde
Liquid hydrogen storage offers substantial volumetric advantages, with density approximately 800 times greater than gaseous hydrogen at atmospheric conditions. This dramatic density increase enables economical long-distance transport and storage of large quantities, though it requires maintaining cryogenic temperatures of -253°C (20K). Industrial gas companies like have developed specialized infrastructure throughout the entire liquid hydrogen value chain, from production and liquefaction to storage, transport, and regasification.
Liquefaction plants represent complex engineering systems that cool hydrogen through multiple stages, typically using a combination of mechanical refrigeration cycles and expansion-based cooling. Modern plants achieve energy consumption of 10-13 kWh/kg hydrogen, though this still represents a significant efficiency penalty – approximately 30% of hydrogen's energy content. Research into magnetocaloric, helium refrigeration, and recuperative heat exchange systems aims to reduce this energy requirement below 7 kWh/kg.
Super-insulated cryogenic tanks employ sophisticated multi-layer vacuum insulation systems that minimize heat infiltration. Despite advanced insulation, heat leakage remains unavoidable, causing gradual hydrogen boil-off at rates of 0.1-0.5% daily in large stationary tanks and slightly higher in transport vessels. Modern systems capture and recompress this boil-off gas, preventing both economic losses and venting to atmosphere.
Transportation of liquid hydrogen occurs via specialized cryogenic trailers and marine vessels. Air Liquide's recent deployment of liquid hydrogen trailers with capacities exceeding 4,000 kg demonstrates the scalability of this approach for regional distribution networks. For international transport, Kawasaki Heavy Industries has pioneered the world's first liquid hydrogen carrier vessel, establishing a supply chain between Australia and Japan that could serve as a model for future international hydrogen trade.
Underground salt cavern storage projects in Texas and Europe
Underground storage in salt caverns offers the largest-scale hydrogen storage solution, capable of containing thousands of tonnes in single formations. Salt caverns are created by solution mining, where water dissolves salt deposits to create large, stable voids with volumes typically ranging from 300,000 to 750,000 cubic meters. The salt provides natural impermeability to hydrogen, while its plastic deformation characteristics help maintain structural integrity under pressure cycling.
Texas has pioneered commercial hydrogen storage in salt caverns since the 1980s, with multiple operational facilities serving petrochemical industries along the Gulf Coast. The Clemens Terminal, operated by ConocoPhillips, represents one of the earliest and largest dedicated hydrogen storage caverns with a capacity exceeding 30 million standard cubic feet. These facilities demonstrate the long-term viability of salt cavern storage, with some installations continuously operating for decades with minimal leakage or structural issues.
European initiatives have expanded rapidly in recent years, with projects in the United Kingdom, Germany, France, and the Netherlands targeting large-scale seasonal storage to balance renewable energy fluctuations. The HyStock project in the Netherlands aims to develop multiple caverns with individual capacities of 300,000-500,000 MWh of hydrogen energy, while Germany's HYPOS initiative is evaluating existing salt structures in central Germany for conversion to hydrogen service. These projects often integrate with broader hydrogen valley concepts that connect production, storage, and diverse end-use applications.
The technical requirements for hydrogen storage in salt caverns differ somewhat from natural gas applications, primarily due to hydrogen's smaller molecule size and different thermodynamic properties. Specialized equipment including hydrogen-compatible compressors, pressure monitoring systems, and specially designed wellheads ensure safe operation. Careful cavern development with appropriate geometry and depth minimizes residual brine and optimizes storage capacity while maintaining geological stability.
Economic considerations favor large-scale, long-duration storage applications where the high initial capital cost is offset by very low marginal storage costs. This makes salt cavern storage particularly valuable for seasonal balancing of renewable energy, strategic reserves, and grid-scale energy management rather than short-term cycling operations. The substantial storage volumes possible in single formations create economies of scale unachievable with manufactured storage systems.
Hydrogen transport networks: HyNet and European Hydrogen Backbone
Hydrogen transport infrastructure represents a critical enabling component for market development, connecting production centers with diverse end users across industrial, transportation, and energy sectors. Pipeline networks offer the most economical transport method for large volumes over land, while specialized shipping solutions enable international trade across maritime routes. The emerging hydrogen economy requires both repurposed existing infrastructure and purpose-built new systems designed specifically for hydrogen service.
HyNet represents one of the most ambitious integrated hydrogen infrastructure projects in the United Kingdom, combining hydrogen production, carbon capture, and pipeline distribution across the industrial northwest. The project plans approximately 350 kilometers of hydrogen pipelines connecting blue hydrogen production facilities with industrial users, power generation, and mobility applications. By targeting an industrial cluster with multiple large-scale consumers, HyNet creates sufficient concentrated demand to justify infrastructure investment while reducing carbon emissions in hard-to-electrify sectors.
The European Hydrogen Backbone initiative presents a continental-scale vision, mapping a potential 40,000-kilometer hydrogen transport network connecting 21 European countries by 2040. This collaborative effort by transmission system operators emphasizes the potential to repurpose approximately 70% of the required infrastructure from existing natural gas pipelines, significantly reducing costs and environmental impacts compared to entirely new construction. The proposed network would create a pan-European hydrogen market connecting major industrial clusters, ports, production hubs, and import terminals.
Technical considerations for hydrogen pipelines include material selection to prevent hydrogen embrittlement, enhanced leak detection systems, and modified compression technologies. Flow characteristics differ significantly from natural gas, requiring recalculation of network capacities and pressure requirements. Despite these challenges, both new construction and pipeline repurposing have demonstrated technical feasibility through projects like the 12-kilometer, 100% hydrogen pipeline operating in the Port of Rotterdam and similar industrial hydrogen networks worldwide.
Fuel cell applications and advancements
Fuel cells represent the most efficient technology for converting hydrogen's chemical energy directly into electricity, achieving electrical efficiencies of 45-60% with virtually zero emissions at the point of use. Unlike combustion engines or turbines, fuel cells operate through electrochemical reactions without moving parts, reducing maintenance requirements and enabling quiet, vibration-free operation. This technology spans applications from milliwatt-scale portable devices to multi-megawatt power plants, with different fuel cell types optimized for specific operational requirements.
Recent technological advances have dramatically improved fuel cell durability, reduced precious metal catalyst requirements, and lowered manufacturing costs through automated production and increased scale. These improvements are driving commercial adoption across multiple sectors, with global fuel cell deployments growing at compound annual rates exceeding 30% in recent years. Material innovations in membranes, catalyst layers, and bipolar plates continue improving performance while simultaneous manufacturing advances reduce costs toward commercial targets.
The integration of fuel cells with hydrogen storage and production creates highly versatile energy systems capable of addressing multiple market needs. In transportation, fuel cell electric vehicles offer rapid refueling and long ranges comparable to conventional vehicles. For stationary power, fuel cell systems provide reliable backup power, grid support services, and combined heat and power in applications ranging from residential to industrial scales. These diverse applications create multiple market entry points for hydrogen technologies, accelerating learning curves and economies of scale.
The remarkable versatility of fuel cell technologies enables a wide spectrum of applications, from powering smartphones and drones to providing primary power for data centers, commercial buildings, and heavy industry. This application flexibility creates multiple pathways for market penetration and technology refinement.
Polymer electrolyte membrane fuel cells for transportation
Polymer Electrolyte Membrane (PEM) fuel cells have emerged as the dominant technology for transportation applications due to their quick start capability, rapid response to changing power demands, and compact design. Operating at relatively low temperatures (60-80°C), these systems achieve impressive power densities exceeding 1 W/cm² while tolerating the frequent start-stop cycles typical in vehicle operations. Their solid polymer electrolyte eliminates corrosive liquid components, allowing operation in any orientation – a critical requirement for mobile applications.
Commercial PEM fuel cell vehicles now demonstrate performance metrics competitive with conventional powertrains, achieving ranges of 400-700 kilometers, refueling times under five minutes, and durability exceeding 20,000 hours in commercial fleet operations. Toyota's Mirai, Hyundai's NEXO, and commercial vehicles from manufacturers including Hyzon and Nikola showcase the technology's maturity. Heavy-duty applications have proven particularly promising, with fuel cell trucks, buses, and trains leveraging hydrogen's high energy density and rapid refueling to overcome the limitations of battery systems in high-utilization, energy-intensive operations.
Technological advances continue reducing system costs through multiple pathways. Catalyst innovations have reduced platinum loadings by over 80% in the past decade while maintaining or improving performance. Manufacturing improvements, including roll-to-roll processing of membrane electrode assemblies and automated stack assembly, have dramatically increased production volumes while reducing labor costs. System integration has simplified balance-of-plant components, eliminating redundant subsystems and optimizing thermal management across the entire vehicle powertrain.
Beyond road transportation, PEM fuel cells are expanding into marine applications, aviation, and off-highway equipment. These sectors benefit from hydrogen's high energy density and the fuel cell's clean, efficient operation. Demonstration projects including passenger ferries in Norway, railway systems in Germany, and aircraft auxiliary power units are validating the technology's versatility across transportation modes. This multi-sector approach creates technology transfer opportunities while establishing diverse market entry points for continued commercial expansion.
Solid oxide fuel cell deployment in industrial power generation
Solid Oxide Fuel Cells (SOFCs) operate at significantly higher temperatures (600-1000°C) than other fuel cell technologies, enabling exceptional electrical efficiencies exceeding 60% in standalone operation. When integrated with heat recovery systems, total system efficiencies can reach 85-90%, surpassing all conventional power generation technologies. These high-temperature systems offer remarkable fuel flexibility, capable of operating on hydrogen, natural gas, biogas, and even some liquid fuels through internal reforming capabilities that leverage their elevated operating temperatures.
Industrial power generation represents an ideal application for SOFC technology, particularly in settings that require continuous baseload operation. Some companies have deployed commercial systems ranging from hundreds of kilowatts to multi-megawatt installations serving data centers, manufacturing facilities, and critical infrastructure. These systems demonstrate electrical efficiencies 20-30% higher than conventional generating technologies while producing significantly lower emissions, even when operating on natural gas inputs.
The gradual transition toward hydrogen-enriched fuels and eventually pure hydrogen operation creates a clear decarbonization pathway for installed SOFC systems. Many current deployments operate on natural gas with 10-20% hydrogen blending capabilities, enabling immediate carbon reductions while maintaining full compatibility with future hydrogen infrastructure development. This "forward compatibility" presents a compelling value proposition for customers seeking to make long-term infrastructure investments amidst evolving energy landscapes.
Technological challenges specific to SOFC systems include thermal cycling limitations, high-temperature sealing requirements, and interconnect durability. Recent materials advances have significantly improved thermal cycling capabilities through modified ceramic compositions and optimized supporting structures that accommodate thermal expansion stresses. Manufacturing innovations, particularly in ceramic processing techniques like tape casting and screen printing, have reduced production costs while improving consistency and durability of critical components.
Alkaline fuel cell systems for stationary applications
Alkaline Fuel Cells (AFCs) represent one of the earliest developed fuel cell technologies, famously used in NASA's Apollo space program to provide both electricity and drinking water for astronauts. These systems employ a liquid potassium hydroxide electrolyte and operate at moderate temperatures (60-70°C), achieving electrical efficiencies of 60-70%. Their relatively simple design and construction using non-precious metal catalysts like nickel and silver offer significant cost advantages over PEM systems, though they require careful management of the corrosive alkaline electrolyte.
Modern AFC systems have largely transitioned to Alkaline Membrane Fuel Cells (AMFCs) that replace the liquid electrolyte with a solid polymer membrane containing fixed alkaline groups. This design innovation eliminates electrolyte management challenges while maintaining compatibility with low-cost catalyst materials.
The tolerance of alkaline systems to lower-purity hydrogen streams presents significant advantages for integration with various hydrogen production pathways. Unlike PEM systems that typically require 99.999% hydrogen purity, alkaline fuel cells can operate effectively with hydrogen purity levels of 95-98%, allowing simplified gas processing and broader compatibility with hydrogen derived from biomass, waste-to-energy systems, or industrial byproduct streams. This compatibility expands deployment opportunities in locations where ultra-pure hydrogen supply chains are not yet established.
Applications particularly suited to alkaline fuel cell technology include backup power for critical infrastructure, off-grid power for remote locations, and maritime installations where cost-effectiveness takes priority over power density considerations. The technology's durability, simplified maintenance requirements, and tolerance to operating environment variations make it especially valuable in challenging deployment scenarios where robust, reliable operation outweighs the advantages of more compact but sensitive alternatives.
Direct methanol fuel cells and portable power solutions
Direct Methanol Fuel Cells (DMFCs) offer a unique approach to portable power by utilizing liquid methanol fuel directly without requiring a separate reforming step. This technology operates at low temperatures (20-90°C) with a polymer electrolyte similar to PEM fuel cells but modified to function with methanol rather than hydrogen. The liquid fuel provides substantial advantages for portable applications, offering energy densities 5-10 times greater than advanced lithium batteries and instant refueling through simple cartridge replacement rather than time-consuming recharging.
Commercial DMFC systems have found market niches in specialized portable power applications including military field power, remote monitoring stations, and extended-duration backup systems. These systems excel in scenarios where grid connection is unavailable and solar power is insufficient or unreliable due to location or weather conditions.
Technical challenges specific to DMFC technology include methanol crossover through the membrane, which reduces efficiency, and relatively low power densities compared to hydrogen PEM systems. Recent material advances in membrane development have significantly reduced crossover effects through modified polymer structures and composite materials that selectively block methanol transport while maintaining proton conductivity. Catalyst developments have improved methanol oxidation kinetics while reducing precious metal content through alloying and nanostructured designs.
While not directly hydrogen-powered, DMFC technology complements broader hydrogen ecosystems by addressing portable applications where direct hydrogen storage presents challenges. Methanol itself can be produced renewably from hydrogen and captured carbon dioxide, creating a carbon-neutral liquid fuel that leverages existing liquid fuel infrastructure. This approach offers a near-term pathway for introducing fuel cell technology into consumer applications while hydrogen infrastructure develops for larger-scale deployments.
Hydrogen economy market development and case studies
The global hydrogen market is undergoing a profound transformation from an industrial commodity to a central energy vector in decarbonized economies. Current global dedicated hydrogen production exceeds 70 million tonnes annually, primarily serving ammonia synthesis, petroleum refining, and chemical manufacturing. However, the emerging clean hydrogen market extends far beyond these traditional uses, encompassing energy storage, transportation fuels, industrial heat, power generation, and building heating applications. Investment commitments in hydrogen projects have accelerated dramatically, with more than $500 billion announced globally through 2030.
Regional hydrogen strategies vary significantly based on resource availability, existing infrastructure, and industrial composition. Countries with abundant renewable resources like Australia, Chile, and Morocco are positioning as potential hydrogen exporters, developing massive green hydrogen production projects. Nations with extensive natural gas infrastructure and geological storage potential, including the United States, Canada, and Norway, are advancing blue hydrogen alongside green pathways. Highly industrialized regions with limited domestic energy resources, such as Japan, South Korea, and Germany, are establishing import strategies and international partnerships to secure future hydrogen supplies.
Industrial clusters represent particularly promising hydrogen deployment zones due to concentrated demand, existing infrastructure, and operational expertise. The H2 Hub Rotterdam in the Netherlands exemplifies this approach, integrating hydrogen production with industrial applications across refining, chemicals, and steel manufacturing while connecting to broader European hydrogen networks. Similar developments are advancing in industrial centers worldwide, including the Gulf Coast Hydrogen Hub in the United States, Japan's Fukushima Hydrogen Energy Research Field, and South Korea's Ulsan Hydrogen Industrial Complex.
Mobility applications are creating market entry points through captive fleet deployments where vehicles return to central refueling facilities, addressing early infrastructure limitations. Public transport bus fleets in Europe, China, and California demonstrate this approach, with hundreds of fuel cell buses now in daily operation. Material handling has emerged as another early commercial success, with over 50,000 fuel cell forklifts operating in warehouse applications where their rapid refueling and consistent power output overcome battery limitations in high-utilization operations.
Environmental impact and carbon intensity analysis
The environmental benefits of hydrogen energy systems depend critically on production pathways, with lifecycle emissions varying by orders of magnitude across different methods. Green hydrogen produced via renewable-powered electrolysis achieves lifecycle carbon intensities as low as 0.5-2 kg CO₂e per kg hydrogen, primarily from manufacturing impacts of equipment rather than operational emissions. Blue hydrogen with advanced carbon capture can achieve 2-5 kg CO₂e per kg hydrogen when incorporating comprehensive capture systems and addressing upstream methane emissions. By contrast, conventional grey hydrogen from unabated natural gas reforming typically generates 9-12 kg CO₂e per kg hydrogen.
Water consumption represents another significant environmental consideration, particularly for electrolytic hydrogen production. Direct process requirements are approximately 9 kg water per kg hydrogen, though actual consumption varies with system design and local conditions. While this direct consumption is modest compared to many industrial processes, the water requirements for electricity generation – particularly cooling needs for thermal plants – can significantly increase the total water footprint of hydrogen production. Renewable-powered electrolysis using wind and solar photovoltaics minimizes this indirect water consumption compared to other electricity sources.
Land use impacts vary dramatically across production pathways. Solar-powered hydrogen production typically requires the largest land footprint, approximately 10-15 hectares per megawatt of electrolyzer capacity, though floating solar and dual-use agrivoltaic approaches can mitigate this impact. Wind-powered production reduces land requirements by 80-90% through spacing turbines and maintaining land availability for agriculture or other purposes between installations. Centralized production from natural gas with carbon capture requires minimal land for the production facility itself but entails broader impacts from resource extraction and carbon dioxide transport and storage infrastructure.
Full lifecycle assessment beyond carbon emissions reveals additional environmental considerations including material resource demands, particularly for electrolyzer manufacturing. PEM systems require platinum-group metals and titanium components, while alkaline systems utilize nickel and stainless steel materials. The substantial global scale-up projected for hydrogen production raises questions about critical mineral supply chains and potential resource constraints. Research into reduced precious metal catalysts, material recycling pathways, and alternative material systems aims to address these concerns as deployment accelerates.